All about Alcast Company
All about Alcast Company
Blog Article
The Ultimate Guide To Alcast Company
Table of ContentsThe 4-Minute Rule for Alcast CompanyAll about Alcast CompanyThe smart Trick of Alcast Company That Nobody is DiscussingThe Of Alcast CompanyThe 5-Minute Rule for Alcast Company6 Simple Techniques For Alcast Company
The refined distinction hinges on the chemical material. Chemical Contrast of Cast Aluminum Alloys Silicon advertises castability by reducing the alloy's melting temperature and improving fluidity throughout casting. It plays a vital function in permitting complex mold and mildews to be filled precisely. Additionally, silicon adds to the alloy's toughness and put on resistance, making it important in applications where longevity is important, such as auto components and engine elements.It likewise improves the machinability of the alloy, making it simpler to process into completed products. In this means, iron adds to the general workability of aluminum alloys.
Manganese adds to the toughness of aluminum alloys and improves workability (aluminum casting company). It is frequently made use of in wrought light weight aluminum items like sheets, extrusions, and profiles. The visibility of manganese help in the alloy's formability and resistance to cracking throughout manufacture processes. Magnesium is a lightweight element that provides strength and impact resistance to aluminum alloys.
The smart Trick of Alcast Company That Nobody is Talking About
Zinc improves the castability of aluminum alloys and aids control the solidification process during casting. It enhances the alloy's toughness and solidity.
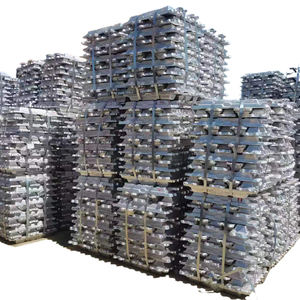
The main thermal conductivity, tensile toughness, return toughness, and prolongation differ. Among the above alloys, A356 has the highest thermal conductivity, and A380 and ADC12 have the cheapest.
The 4-Minute Rule for Alcast Company
In precision casting, 6063 is appropriate for applications where detailed geometries and premium surface finishes are vital. Examples include telecommunication units, where the alloy's remarkable formability enables streamlined and aesthetically pleasing styles while keeping structural integrity. In a similar way, in the Lighting Solutions industry, precision-cast 6063 components develop classy and efficient lighting components that require detailed forms and good thermal performance.
It leads to a finer surface area coating and better corrosion resistance in A360. The A360 exhibits remarkable elongation, making it ideal for complex and thin-walled parts. In accuracy casting applications, A360 is appropriate for markets such as Consumer Electronics, Telecommunication, and Power Tools. Its improved fluidness enables elaborate, high-precision elements like smart device casings and communication tool housings.
Get This Report about Alcast Company
Its one-of-a-kind properties make A360 a useful option for accuracy casting in these markets, improving product durability and top quality. Aluminum alloy 380, or A380, is a commonly utilized casting alloy with several distinctive features. It offers outstanding castability, making it an ideal choice for accuracy casting. A380 shows great fluidness when molten, making sure elaborate and comprehensive molds are accurately recreated.
In accuracy spreading, aluminum 413 radiates in the Consumer Electronic Devices and Power Tools markets. It's frequently made use of to craft complex components like smart device real estates, cam bodies, and power tool casings. Its precision is impressive, with tight tolerances as much as 0.01 mm, making certain flawless product setting up. This alloy's exceptional rust resistance makes it a superb choice for outside applications, guaranteeing resilient, long lasting items in the stated sectors.
How Alcast Company can Save You Time, Stress, and Money.
As soon as you have chosen that the aluminum die casting procedure is suitable for your job, an important next action is selecting one of the most suitable alloy. The light weight aluminum alloy you pick will significantly influence both the spreading process and the buildings of the end product. Due to the fact that of this, you must make your decision thoroughly and take an enlightened strategy.
Identifying the most appropriate light weight aluminum alloy for your application will indicate weighing a broad variety of characteristics. The initial group addresses alloy features that affect the production process.
The Basic Principles Of Alcast Company
The alloy you choose for die spreading directly affects a number of facets of the casting procedure, like exactly how easy the alloy is to function with and if it is susceptible to casting defects. Warm cracking, additionally referred to as solidification cracking, is a regular die casting defect for light weight aluminum alloys that can result in inner or surface-level tears or cracks.
Particular aluminum alloys are a lot more at risk to hot fracturing than others, and your choice should consider this. An additional usual issue discovered in the die spreading of aluminum is die best site soldering, which is when the cast stays with the die walls and makes ejection hard. It can harm both the cast and the die, so you must seek alloys with high anti-soldering residential or commercial properties.
Corrosion resistance, which is currently a noteworthy quality of aluminum, can vary considerably from alloy to alloy and is a necessary particular to consider depending on the environmental problems your item will certainly be revealed to (aluminum metal casting). Wear resistance is one more home frequently looked for in aluminum products and can separate some alloys
Report this page